|
|
Facilities and Equipment
Since 1991, Mission Support has been located at the Freeport Center Building Z-15 in Clearfield Utah. Mission Support has at present 40,000 square feet of leased space for active manufacturing and warehouse space. Mission Support’s facility is an access controlled facility. After working hours, the building is locked and the Freeport Center controls access to the industrial park through a guard station.
The Freeport Center is an industrial complex with over 7 million square feet of leased manufacturing space. About 5% of this space is available for lease at any time. If required Mission Support could easily secure more space from the Freeport Center.
Mission Support has two compressors, a 75 hp Gardner Denver used to run hand tools and a 100 hp Atlas Copco, used to run our plastic media blasting and shot peening systems.
Mission Support has an 80 FT enclosed truck dock with a 10 ton bridge crane. Two automatic dock levelers, and a selection of forklifts. Railroad access is easily accessible to Mission Support.
Mission Support has a 30 by 50 foot paint booth with various methods of overhead material handling capabilities for painting a wide range of parts and assemblies. Our paint booth will move 50,000 CFM of air while in operation and has a 3 million BTU composite air system that can maintain a constant temperature of 70º F. Mission Support has received approval from the Utah State Division of Environmental Quality for painting the majority of military specification paints. The paint booth is annually certified as meeting all of the Utah State standards for emissions. Mission Support is qualified to alodine parts and assemblies IAW MIL-C-5541 also.
|
Mission Support has a MIL-A-8625 compliant chromic Anodizing facility, utilizing a SIFCO anodizing system for precision anodizing, used for the B-52 Bypass Engine Duct program.
Mission Support has a 4800 square foot clean room with temperature, humidity, and dust control systems. The clean room is utilized by the KC-135 Boom Nozzle Assembly, Pratt & Whitney Pressurized Oil Tank, and UH-60 Servo valve programs.
Mission Support has state of the art welding capabilities. Our welder has certifications to AWS D17.1 to Aluminum, Titanium, and Stainless Steel for aerospace applications.
|
Mission Support operates an AAI/ACL Technologies IMAGETM Model 9740-0070 Hydraulic Component Test Stand, and an Avtron H334 Test Stand. The IMAGETM consists of a microprocessor-based Electronics Console and a Hydraulics Console for analyzing complex hydraulic components. The IMAGETM automatically controls the Unit-Under-Test (UUT) current drive signals, conditions the necessary measurement transducers within the test stand, receives the test result signals, performs the commanded versus observed result analysis (hysteresis, linearity, maximum flow, etc.), and prints out the results, including plots, when needed.
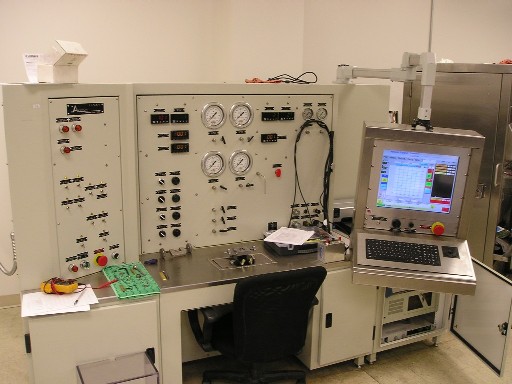
Mission Support also has Certified LabView Engineering Personnel who can design, develop, and build ATP Test Stands to test any Electro-Hydraulic Aircraft components.
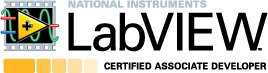
|
|
Mission Support Facilities – Quality Assurance:
-
15’ X 20’ Environmentally Controlled Clean Room
-
48" x 72" x 8" Grade A Granite Surface Plate
-
Faro Platinum and Gold Arms for Precision 3D Inspection and Reverse Engineering
-
OGP Optical Comparator
-
Faro Laser Scanners for Reverse Engineering Capabilities
-
Various Inspection and Reverse Engineering CAD/CAM Software
-
NX, TurboCad and Mastercam CAD Programs for NURB and Solid Modeling
-
Allocated Receiving Inspection Area
-
Govt. Audited MRB Bond Area
-
Precision Air Gaging Systems
See Quality Assurance Link for More Information
|
|
© Mission Support Incorporated 2006 |
|